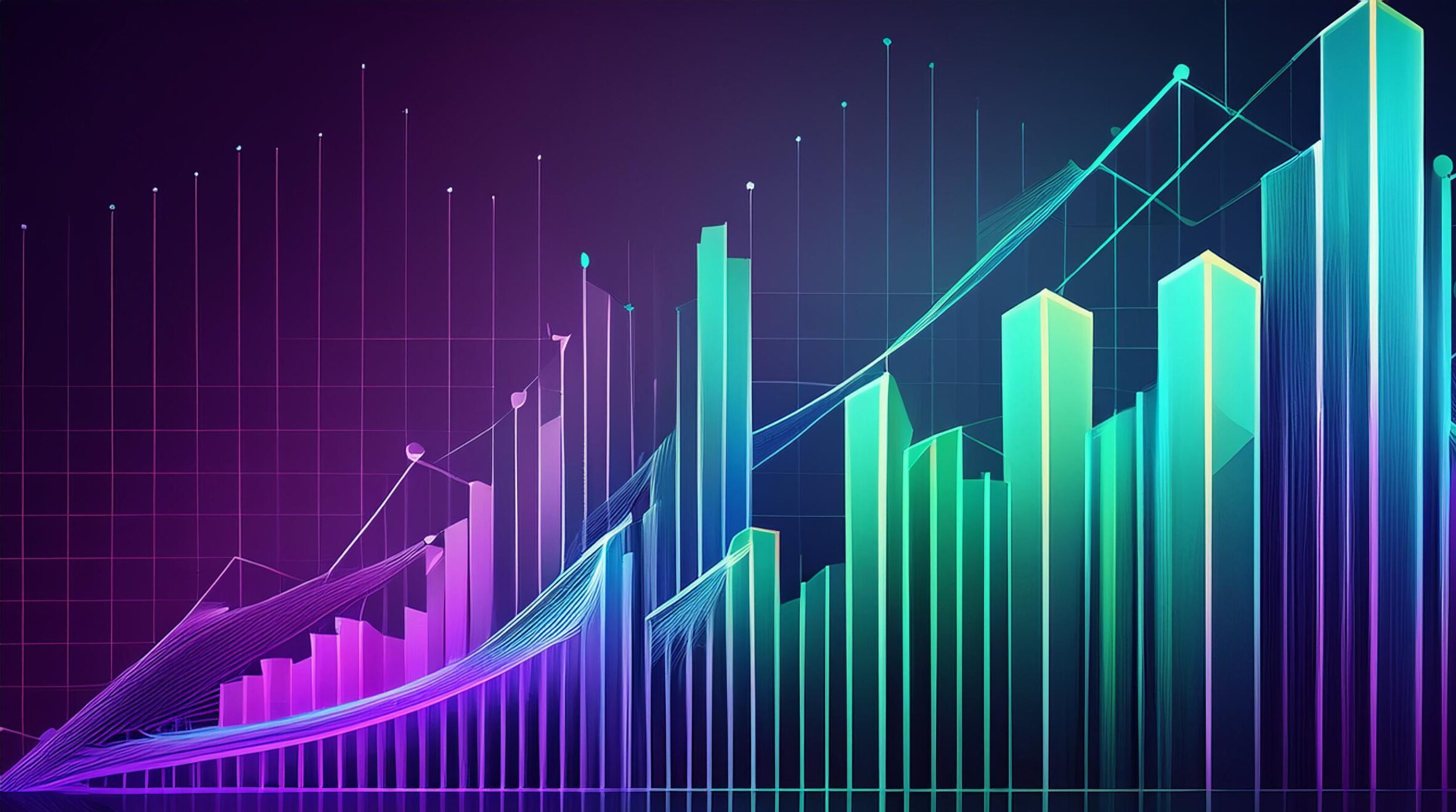
lean six sigma consulting
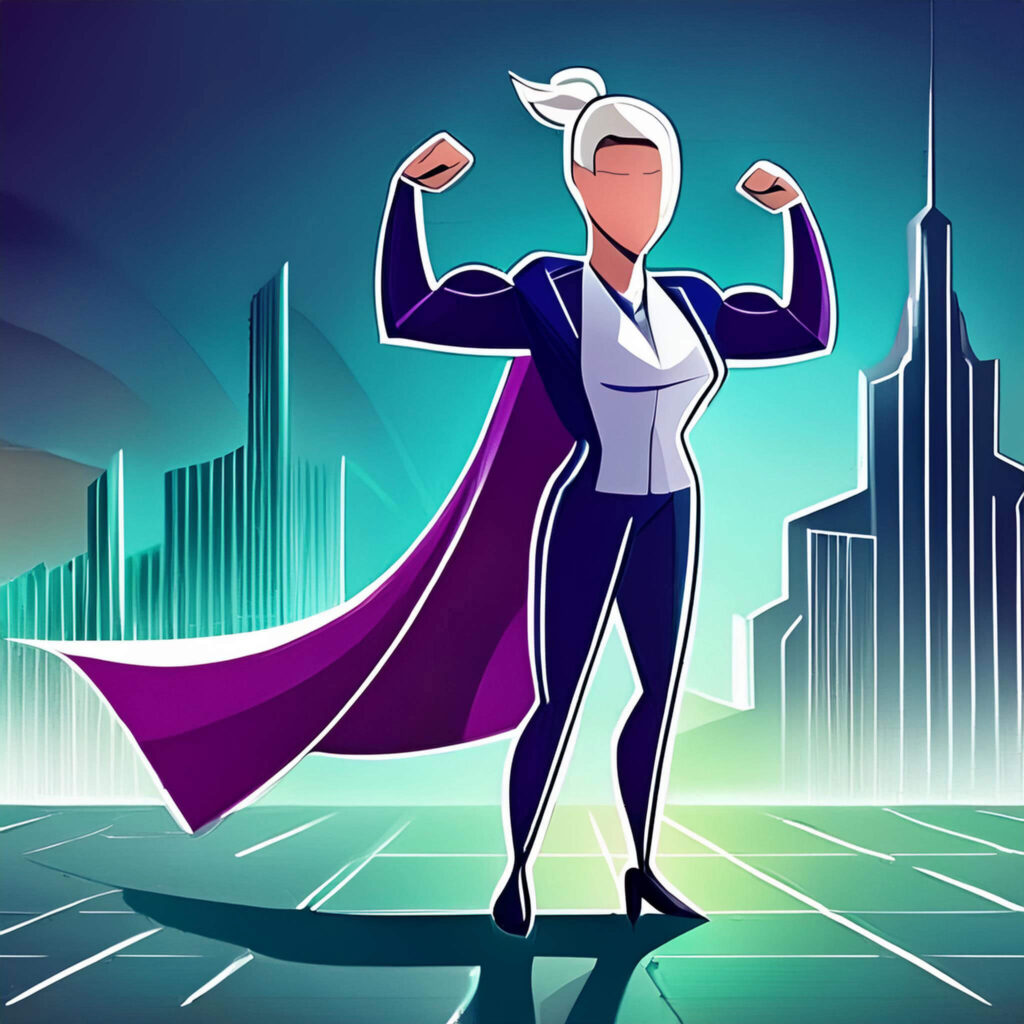
Streamline Your Business for Growth
Tired of inefficiencies, errors, and waste holding your business back? Lean Six Sigma is a proven methodology that helps companies of all sizes optimize their operations, improve quality, and boost profitability. At Data Driven Dynamics, we leverage Lean Six Sigma expertise and AI-powered insights to help you achieve measurable results and unlock your business’s full potential.
What is Lean Six Sigma?
Lean Six Sigma is a proven methodology that empowers businesses to achieve operational excellence and sustainable growth by combining the waste-reducing principles of Lean manufacturing with the rigorous quality focus of Six Sigma.
How Lean Six Sigma Can Benefit Your Business
How Lean Six Sigma Works
Lean Six Sigma projects typically follow a structured five-step process called DMAIC.
- Define: Clearly define the problem or opportunity for improvement.
- Measure: Collect data to establish baseline performance and identify areas of waste.
- Analyze: Analyze the data to pinpoint the root causes of the problem.
- Improve: Develop and implement solutions to address the root causes and improve the process.
- Control: Establish monitoring systems to ensure the improvements are sustained over time.
Lean Six Sigma Tools & Techniques
We utilize a variety of proven tools and techniques to drive your Lean Six Sigma journey:
Our Approach to Operational Excellence
Identify Improvements
We collaborate with your team to identify the most impactful areas for improvement, aligning with your business goals.
Analyze Data
We gather and analyze data to uncover the underlying issues hindering your performance, not just the symptoms.
Implement Solutions
We craft customized strategies and implement practical solutions that deliver real results, not just quick fixes.
Empower
We empower your team with the skills and knowledge to maintain momentum and drive ongoing enhancements long after our engagement.
Ready to transform your business?
Contact us today to learn more about our Lean Six Sigma consulting services and discover how we can help you achieve operational excellence.